Key#1: Understand the regulations that pertain to your industry and your business throughout each level and function of your organization
This is more difficult than it appears because Federal Regulations are simply not prescriptive and that is by design. 21CFR 820 Medical Device QSR for example, must be applicable to both manufacturers of small surgical instruments as well as manufacturers of MRI devices requiring that the regulations be sufficiently vague and flexible to pertain to each product.
At the end of the day, it is the responsibility of every regulated organization to interpret those governing regulations as they pertain to the company’s unique product and processes and apply those interpretations throughout the organization. In most cases, this will require the assistance of outside industry and regulatory experts to make these interpretations and the case for the direction that the company chooses to go.
Certainly the most simplistic solution to achieving compliance excellence is “to do the right things right!” But what does this really mean? I have distilled the “doing the right things right” solution into 7 separate individual keys or actions that will provide a solid foundation for the establishment of any compliance program.
Key#2: Define your critical processes relative to the regulatory path that has been chosen. Many organizations do not adequately define their processes
After choosing a regulatory path, complete and thorough process definitions that are foundational to the business must be developed and validated with linkage to the governing regulations. These process definitions are the first rung on the ladder, the “50,000 ft. view,” the genesis of the operational and regulatory paradigms that will form the structure of how the business will be run in an efficient, effective, and compliant manner.Key#3: Develop sound regulatory documentation
Documentation should not simply meet a regulatory requirement but be designed to effectively direct operations, be foundational to a comprehensive worker training approach, and serve as the basis for a sound continuous improvement process.
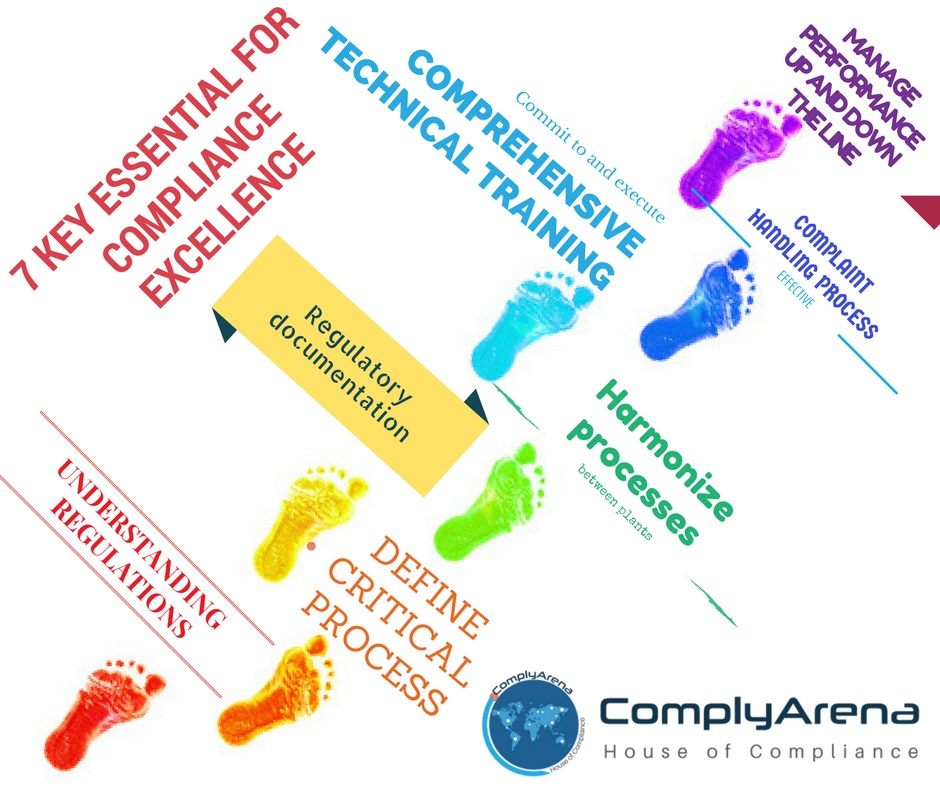
Key#4: Harmonize your processes and procedures between plants
Inconsistency between operations although not necessarily a problem are cause for concern when those inconsistencies are uncovered during an inspection or investigation. Best practices should be determined for “like” operations, equipment, processes, etc. and then implemented across all facilities and locations where those “like” operations exist.Key#5: Commit to and execute comprehensive technical training. Competence is the prerequisite to competition and compliance
“Read and Understand” the most basic of approaches used to transfer “knowledge and skill” in the life sciences today simply does not work. If your goal is to just meet a regulatory requirement, this is as far as you need to go – buy an LMS, build the most basic of technical documentation, assign document readings, roll the regulatory inspection dice, and you are good to go.
If your goal, on the other hand, is to create an organization that meets or exceeds your regulatory responsibilities, demonstrates operational excellence, develops and deploys superior competence, and truly demonstrates the attributes of a learning organization, you must invest in training infrastructure, organizationally support training, provide training a seat at the operations and regulatory tables and include the function in the decision-making and advisory processes, and consistently execute an effective training process for both new and existing human resources.
Key#6: Institute a sound and effective complaint and investigations handling process :
Looking at a history of 483 observations and warning letters will tell you that CAPA deficiencies uncovered during FDA investigations consistently rank in the top three of the reasons for triggering a 483 warning letter. It is essential that CAPA systems and processes be fully integrated with corporate strategies and policies and there be a commitment up and down the organizational structure to fully execute the process.Key#7: Manage performance up and down the line to the performance structure created. If it is not managed it will not be performed
Junior level managers and supervisors and the workforce in-general for that matter, must never be given cause to think that circumventing or ignoring a process or a step to a procedure is acceptable behavior even if it impacts throughput, schedules, or the “bottom-line.” The risks to patient and end-user health and safety are simply too great. Regulatory compliance must be sacrosanct and an enforceable component of the performance management system. That message must be sent and received throughout the organization.
The intent of this approach is to demonstrate linkage between each level beginning with the regulatory requirements themselves through regulatory documentation, through the training process, ending ultimately with the management of individual human performance.